Delve into the enlightening journey of Boender & Beutel as they navigate the intricate process of attaining GOTS certification. Christian Zaudig, the key figure spearheading the certification process at the company, sheds light on the motivations, challenges, and implications of their quest for this renowned sustainability seal in an engaging interview. Join us as we unpack this candid conversation, offering a nuanced understanding of the company’s commitment to sustainability and its transformative journey towards a greener future.
In the global quest for sustainable manufacturing practices, the Global Organic Textile Standard (GOTS) stands as an unerring beacon, guiding textile companies towards a path of ecological responsibility and social ethics. Acquiring this highly coveted certification, however, is a tale of tenacity, commitment, and unwavering dedication to the pursuit of sustainability. Christian Zaudig, a senior project manager at Boender & Beutel, recounts this intriguing odyssey, revealing the company’s inspiring journey towards achieving the GOTS certification.
Nils: Hey, Chris! It’s great that you’re taking the time. Who are you and what do you do at Boender & Beutel GmbH?
Chris: My name is Christian Zaudig, and I am the Senior Project Manager and Purchasing Manager at Boender & Beutel. I began my career as a media design apprentice in a textile printing operation and later worked at KOMA-Merchandising GmbH (now a brand of Boender & Beutel) as a graphic artist and clerk. There, I eventually became the operations manager. Afterward, I transitioned to Boender & Beutel and have been a witness to, and shaper of, the company’s growth. My responsibilities include operational purchasing for #PrintonDemand merchandise and overseeing the certification processes.
“We want to create a fair and sustainable working environment.”
Speaking of which! Why did we actually pursue GOTS certification?
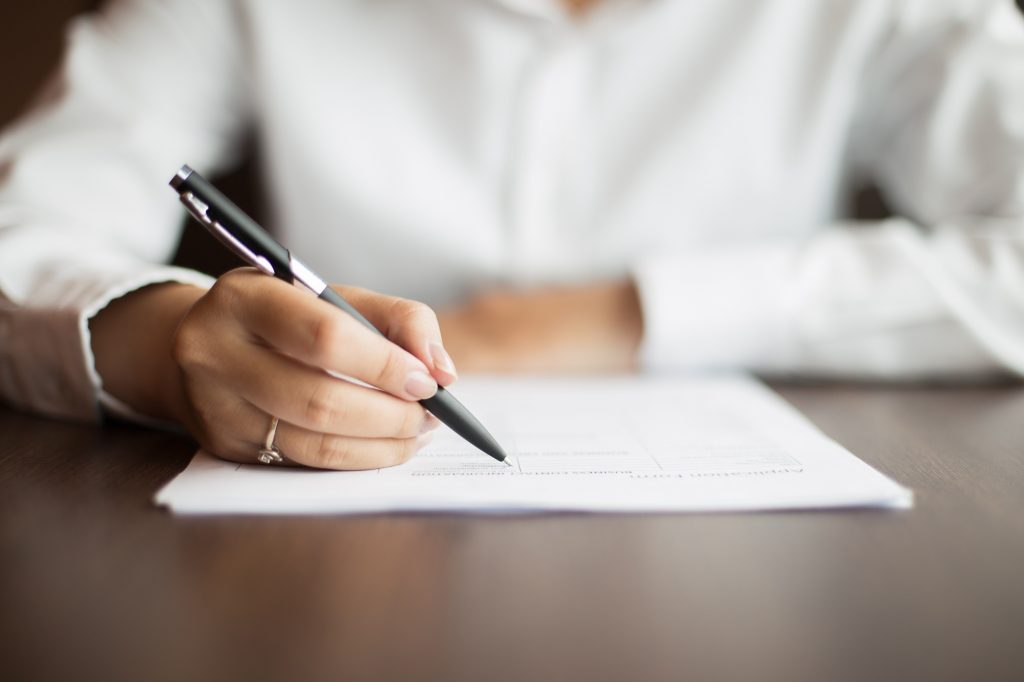
Given our growth and our focus on sustainability and quality, certifications have become increasingly important to us. One of our main suppliers, Stanley/Stella, which also emphasizes sustainability and quality, inspired us to align with appropriate standards and initiate certification processes. The motivation for GOTS certification was the chance to secure a high-quality and stringent label that minimizes room for greenwashing. We wanted not only our products but also our company as a whole to be certified. Thus, the customer receives a consistently certified product. The Global Organic Textile Standard gGmbH includes, among other things, pollutant-free production, the use of organic cotton, and high social and compliance standards. We also aimed to create a fair and sustainable working environment by adhering to the GOTS guidelines. We sought not only to offer certified products but also to implement certified processes and structures.
How did the certification process unfold?
The initial audit was conducted in 2020 by CERES – Certification of Environmental Standards GmbH, an auditor authorized by GOTS. After our first contact with CERES, an interview and a proposal for the audit followed in 2020, which was then carried out onsite. Subsequently, a report was written and handed over by the auditor to an internal evaluator. From my perspective, the process was very well protected against corruption. After the evaluation, we received a deviation letter with deadlines, outlining the measures that must be implemented in the company to meet the GOTS guidelines. We established and documented the corresponding processes, which had not been previously documented in writing. Many of the guidelines we had already met, but they weren’t documented to ensure their measurability. These were both social and environmental guidelines. Thus, we fulfilled all GOTS requirements and received the GOTS certificate for the first time in 2020. Now, we are listed in the GOTS database as a certified company.
After an elaborate but necessary process, we earned our certification. How did things proceed from there?
There is an annual re-audit, which checks whether we are still meeting the (occasionally updated) guidelines. The advantage of certification and standardization is that we agree on a set of rules in collaboration with the standard setters in order to jointly achieve sustainable and high-quality work. The standard goes beyond legal requirements and thus ensures superior processes and products. Examples of social standards include the existence of an internal anonymous complaint system and ensuring a livelihood-securing salary in the respective region, instead of merely paying the minimum wage.
We now have the opportunity to further process and sell GOTS-certified products according to GOTS guidelines. How can business customers have their products certified according to GOTS by us?
If a business customer wants to sell GOTS-designated goods themselves, we first create an offer. When an order is placed, we then request a transaction certificate (TC) from our supplier to ensure the GOTS-compliant supply chain. These TCs ensure that the products meet the GOTS product criteria. We issue the customer an invoice and validate the supply chain using the TCs. If we, at Boender & Beutel GmbH, take over the fulfillment in our name, the process is as described. If a company issues the invoice to its customers itself and acts as the last part of the supply chain, it must become GOTS certified. For this, so-called operation certificates, the second pillar of the GOTS certificates, must be obtained. These ensure that an operation itself meets the criteria (such as social standards) for processing GOTS products.
“Our awareness of the importance of certification for both our company and our customers has sharpened.”
What has changed in the company as a result of the certification?
In fact, we were very close to meeting the standard even before the certification. There was practically nothing that would have been a criterion for exclusion from the label. We have always been a modern and conscious company that values sustainability, social compatibility, and quality. However, what has changed is that we now have documented processes, making them more measurable and transparent. Also, our awareness of the importance of the certification for both our company and our customers has heightened. We have evolved over the last few years, and the certification was another significant step towards sustainability and quality.
So, what’s next?
We aim to expand our certifications in the next few years. Another goal is to attain full GOTS certification in the area of Print-on-Demand. This means that not only the products but also the entire supply chain, including our print shop and our partners, must be GOTS certified. We want to ensure that our customers receive high-quality and sustainable products that meet the highest standards from raw material extraction to production. In addition, we plan to further expand our partnerships with GOTS-certified suppliers to offer an even wider range of sustainable materials and products. Sustainability is and will remain an important part of our corporate strategy, and we will continue to work on continuously improving our processes and products.
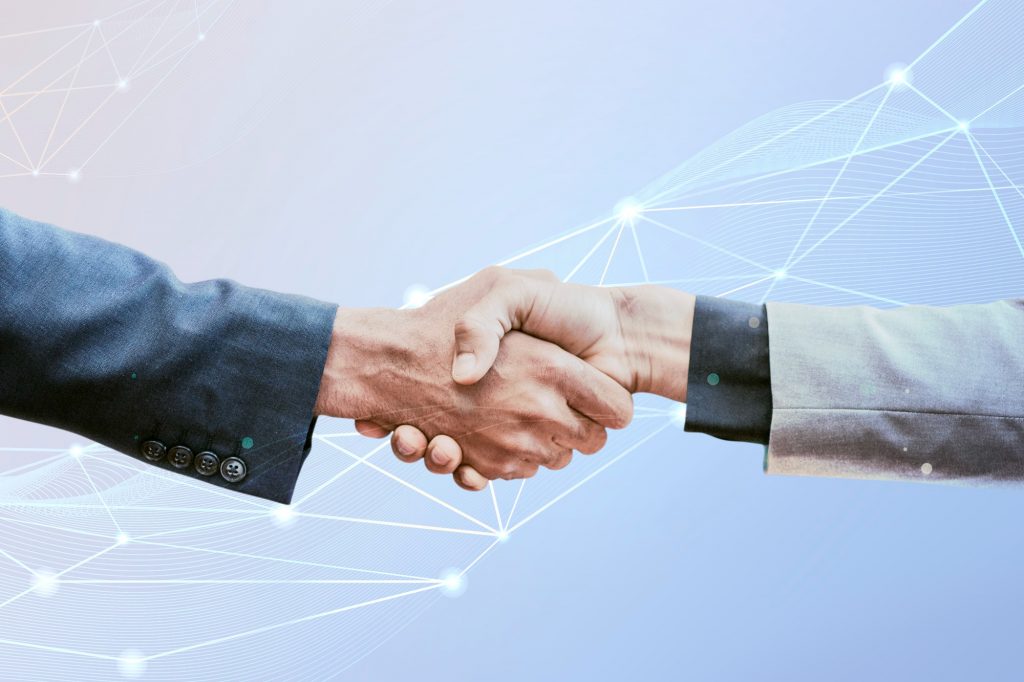
Thank you for the interview and the interesting insights!
You’re welcome. It was a pleasure to talk about our experiences with GOTS certification. I hope that we can encourage other companies to embark on the path of sustainability and seek certification. Together, we can make a positive contribution to the environment and society.